3秒で理解!このコラムで分かること
製造業の収益性改善には、従来の資材購入原価に基づく原価計算から、生産活動別の原価把握へと視点を転換し、経営と現場の物差しを統一することが重要。
#BIZXIM製番 #製番とは #収益性改善 #原価計算
1.原価計算の物差し
生産改善に取り組まれる管理者は、製品の収益性改善にあたっては左の図表1と右の図表2とではどちらを活用されるでしょうか?恐らく直感的には右側の図表2を選択されるのではないかと考えます。両者とも売上高は100円、売上原価は80円、粗利益は20円で、何も変わりがないように見えますが、左図表1では80円の売上原価の内容が、製品を作るのに必要な生産資源(材料、労働費、経費)別の調達購買原価で測定されています。
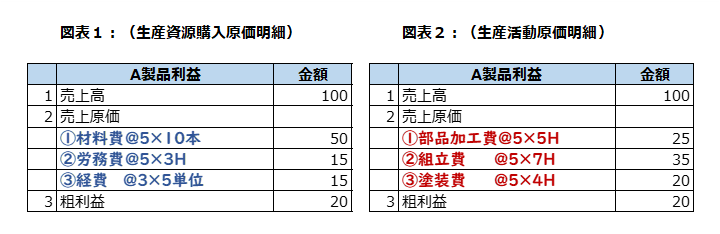
一方、図表2の売上原価の明細は、部品加工や、組立、塗装などの生産加工活動の内容別に原価を集計した図表になっています。生産改善に取り組まれる担当者は、調達資源の購入代も重要ですが、加工活動の原価がより関心が高いと思われるので、右の図表2を選択されるだろうと考えるわけです。
両者の原価の違いは何でしょうか?
原価は80円、粗利益は20円で同額ですが、原価を測定する尺度が根本的に違っています。右の図表2の測定尺度は生産活動そのものであるのに対して、左の図表1は生産資源の購入対価を測定しています。仮に左図表1を使う場合に生産改善で検討出来ることはモノや人や外部サービスを如何に安く入手できるかだけです。
一方、右図表2による生産改善では、生産工法を如何に工夫すれば廉価な原価で生産できるのかの検討です。
しかし、製造業における原価計算は、左図表1の生産財の原価を測定するものとして昭和37年に定められた原価計算基準で定められていますので、経営者や経理関係者は55年以上も、この基準にならされているので原価計算、利益改善と言えば、左図表1がすべてであるとする発想が染みついています。
結果、社内の上意下達は殆どがこの一律な基準で浸透しているのが現状です。
しかし、上意下達はそうであっても、企業内で製品開発や生産管理部門でコストダウンを測る手法は必ずしもそうではないでしょう。
製品開発や生産改善担当の方々は、既定の原価計算表の様式にかかわらず、右図表2の生産活動の視点で日々コストダウンを追求しているはずです。即ち経営の物差しと生産部門の物差しの次元が違っているのです。しかし物差しが違っていることに気が付いている企業は意外と少ないのです。
本コラムで提示させて頂くのは、製造業の収益性を追求する原価計算と生産性の改善を図る尺度や情報が、ばらばらで統合化ができていないということです。55年間の原価計算基準に愚直に従うことで製品原価の物差しは生産資源の購入代だけに染みついてしまっているのです。
2.原価計算の物差しが、資材購入原価であることの弊害
前述の様に、原価計算の物差しが、材料、労務、サービス(経費)の購入代を一義として測ることに終始していることが様々な局面で製造業の収益性改善活動を阻害します。
1)収益性改善に必要な生産活動の現状把握と改善検討に必要な情報は現在の原価計算で完結済みとの思い込みが組織に定着し、今の原価情報の枠外から収益性向上に有効に役立てる情報活用をしようという発展的な思考が生まれません。
2)生産資源の購買原価測定という従来型原価計算は、経理部門や購買部門の専管領域という固定概念が社内に定着し生産改善を司る開発生産部門の原価に関する関与や関心を希薄にしています。
3)利益向上=原価削減=購買コスト削減というような発想が固定化され、開発プロセスの変革、工程再編、生産リードタイム短縮、品質管理精度向上といった生産視点での収益性改革は技術の問題というように経営管理層から切り離されている組織風土が多く見られます。