3秒で理解!このコラムで分かること
製番ごとにE-BOMを管理し、M-BOMは共通・オプション部品に分けて簡素化。在庫の過不足を製番間で調整し、生産効率と在庫精度の向上が可能。
#BIZXIM製番 #製番とは #受注生産
前回の「MRPと製番管理2:製番管理とMRPの混在のための工夫」で指摘した運用上の留意点について説明します。
1.部品表の持ち方に関する留意点
個別受注生産では製番ごとに異なった仕様のため受注ごとに設計が行われ、製番別のBOMが次々と作られBOMが爆発して管理しきれなくなることがあります。
一方通常個別受注生産のBOMは設計と生産が同時並行的に行われるため、E-BOMとM-BOMは同じで、製品の技術情報として一緒に出荷されますので製番別のBOMも必要になります。
ここでの課題はE-BOMは製番別で持ちますが、M-BOMを簡素化できないかというテーマに言い換えることが出来ます。
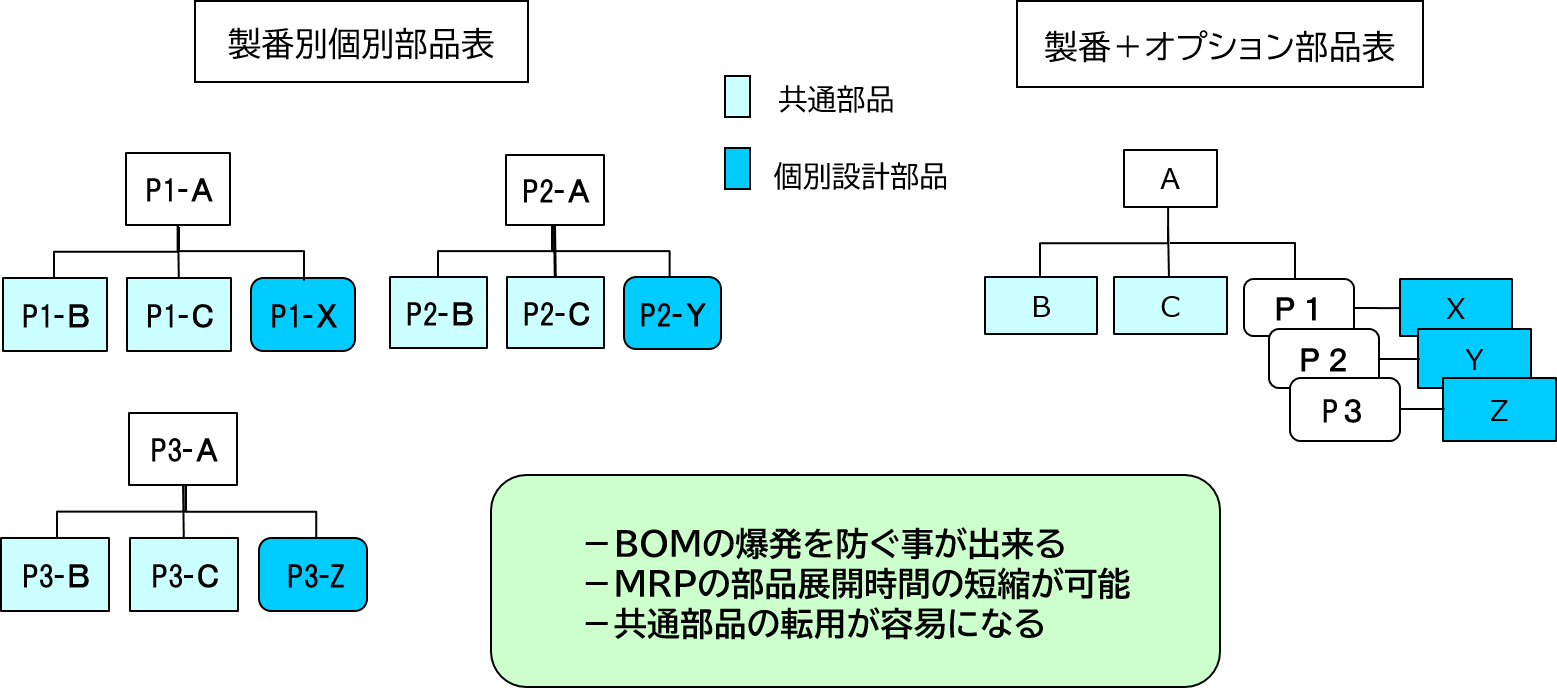
共通機能部分とカスタマイズ機能部分(図のⅩ、Y、Z)がうまく分けられるならば有効な方法ですが、設計の初期段階から意図的にアーキテクチャー(設計思想)として取り組む必要があり、容易に出来るわけでは有りませんが、生産設備メーカ等で製番管理を使用しているところではこのような形の設計を行い、個別受注生産でありながらCTO(受注仕様生産)で対応しているところも多く見受けられます。
個別受注生産とはいえ機種やモデルが同じ場合は共通部分も多く、実際の設計作業では似たような製品の図面を元に手直しを加える流用設計が行われており、その場合は比較的容易に上図右側の「製番」+「オプション」部品表にすることが可能です。
そのためにはまず機種、モデルごとの標準部品表を作っておきます。
上図右側で部品BとCだけで出来た製品A用BOMを持つということで、受注仕様に基づき製番ごとにⅩ、Y、Zといったオプション機能を作図し追加してM-BOMを作ります。
部品BとCは同じ機種、モデル内では共通ですので先行手配や半製品としてまとめて生産することも可能です。
その後オプション部分の設計が完了したところで材料を手配し最終組み立てをすれば完了です。
製品が完了したところでBOMの展開機能(一般的な正展開機能)で上図左側の「製番別個別部品表」を作り、納入時に技術情報の一部として出荷します。
これでテーマであるE-BOMは製番別で持ち、M-BOMを簡素化することが出来ました。
2.余剰在庫の管理方法と引当方法に関する留意点
▼ 製番別在庫管理と余剰の引当機能概要 ▼
製番管理における在庫管理上の留意点
製番管理では同一品番のものであっても需要も供給も製番別に引き当てが行われる為、変更等の理由で過不足が起きた場合でも製番を超えて製番間での転用は非常にやりにくくなっています。
そうは云っても現場の知恵で担当者同士で融通しあい貸し借りを行って無駄をなくしていることが多々あるようですが、システムを通さないやりくりのためはっきりした決まりも無く時間がたつと徐々に曖昧になるケースが多々発生し、在庫精度が悪くなることがあります。
これを防ぐ工夫として製番別過不足情報管理の仕組みを持つことが考えられます。
もともと製番ごとの需要に基づいて調達が行われていますので余剰が発生する余地はないはずですが変更等により当初の予定とは違って、過不足が発生する事もあるでしょう。
足りない場合は緊急オーダで対応しますが、余った部材はそのままにしてしまうケースが多いようです。
製番間の過不足を調整する機能があると便利ですが、本来製番管理の基本概念が製番間では相互不可侵と云うことですので本来的にはありえない機能ですが必要に応じて過不足の調整を製番間で行うシステム支援が可能です。
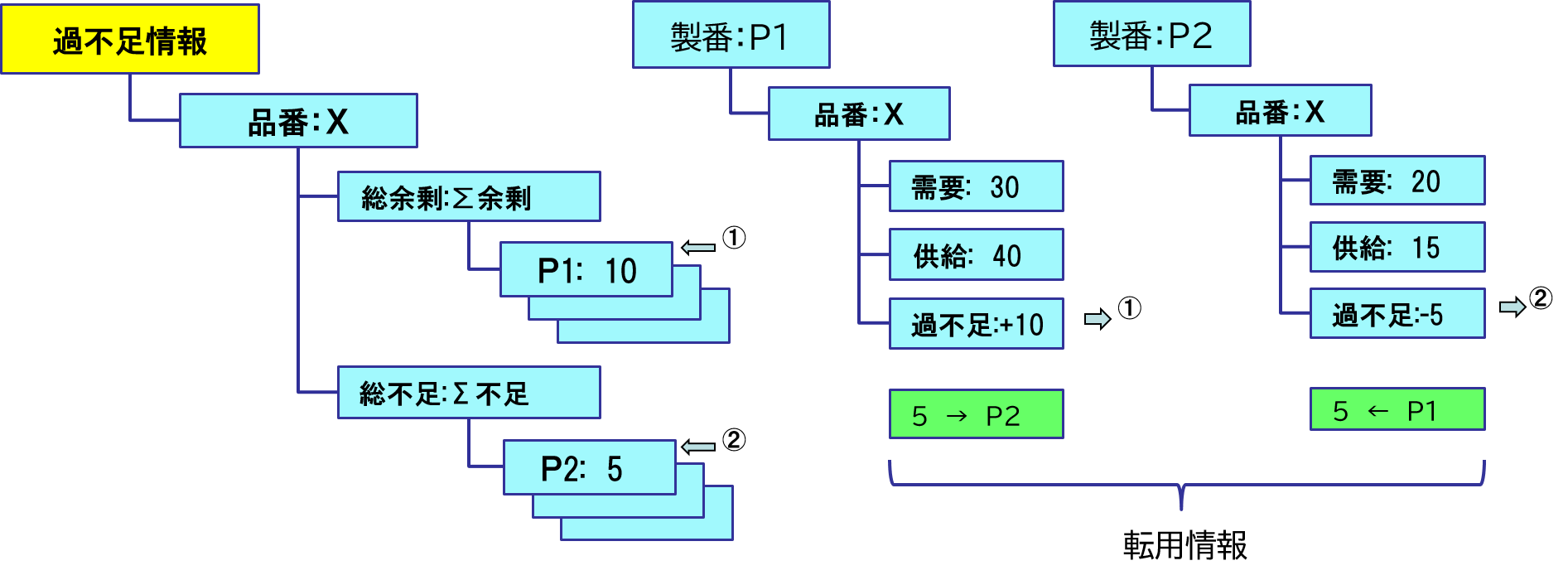
上図のように基本的には需給は製番別に分かれて管理されていますがそこに過不足情報を付加する事により製番を超えた転用が可能になります。(図の①と②)
このとき注意すべき点は製番間の引渡しと引き受けの情報を明確に記録しておき何か問題があった時に簡単に元に戻せるようにしておく必要があります。(図の転用情報)
上図では省略しておりますがそれぞれの過不足情報も転用にあわせて更新します。
このあたりの運用上の合意がないと担当者は転用を好まず、この機能はうまく使われないようです。
3.製番管理とMRPのまとめ
「製番管理」と「MRP」は決して対立する概念ではなく、製品の特質によりどちらが適しているかと考えるほうが正しい判断が出来ると思います。簡単に言うと量産もので共通部品が多いものは「MRP」向きで、個別一品生産のように受注ごとに仕様が異なるものは「製番管理」向きといえると思います。
又機能的には類似点も多く全く別なシステムが必要というわけではないこともご理解いただけたと思います。
最後にここでの説明内容ですが、この方法しかないとか、どのパッケージにも同様の機能があるということではありません。
お客様の課題が何かということを、より具体的に説明しようと思い細かい話になってしまいました。その点ご理解いただければ幸いです。