3秒で理解!このコラムで分かること
製番管理は、製造手配時に管理番号を付与して一貫管理する方式であり、MRPと異なる管理単位を持つが、両者を組み合わせた運用も可能。
#製番管理方式 #BIZXIM製番 #製番とは
1.製番管理とは
製番管理方式とは、製造手配時に「製番」 と呼ばれる管理番号を設定し、計画・発注・出庫・作業指示から出庫までの全作業をこの製番で管理する仕組みです。
設計の前提条件は商品企画や個別受注における顧客要望機能・条件(要件)です。(下図左の領域)
ここが適切に設定できないと、いくら設計が頑張っても売れる商品にはなりません。市場に立脚した情報を管理し、売れる商品の要件を詰めることが可視化の最初の作業です。良い製品設計のためには、顧客要望機能・条件とその根拠を残しておくことです。これをもとにマーケティング検証を行い、継続的に強い商品に育成していくべきです。また受注設計型製造業の営業部隊は、このシートを持ち左側の顧客要望を確認していくとよいでしょう。この要件の体系化とバリエーションのコントロールをしていくと量産効果につながるようになります。
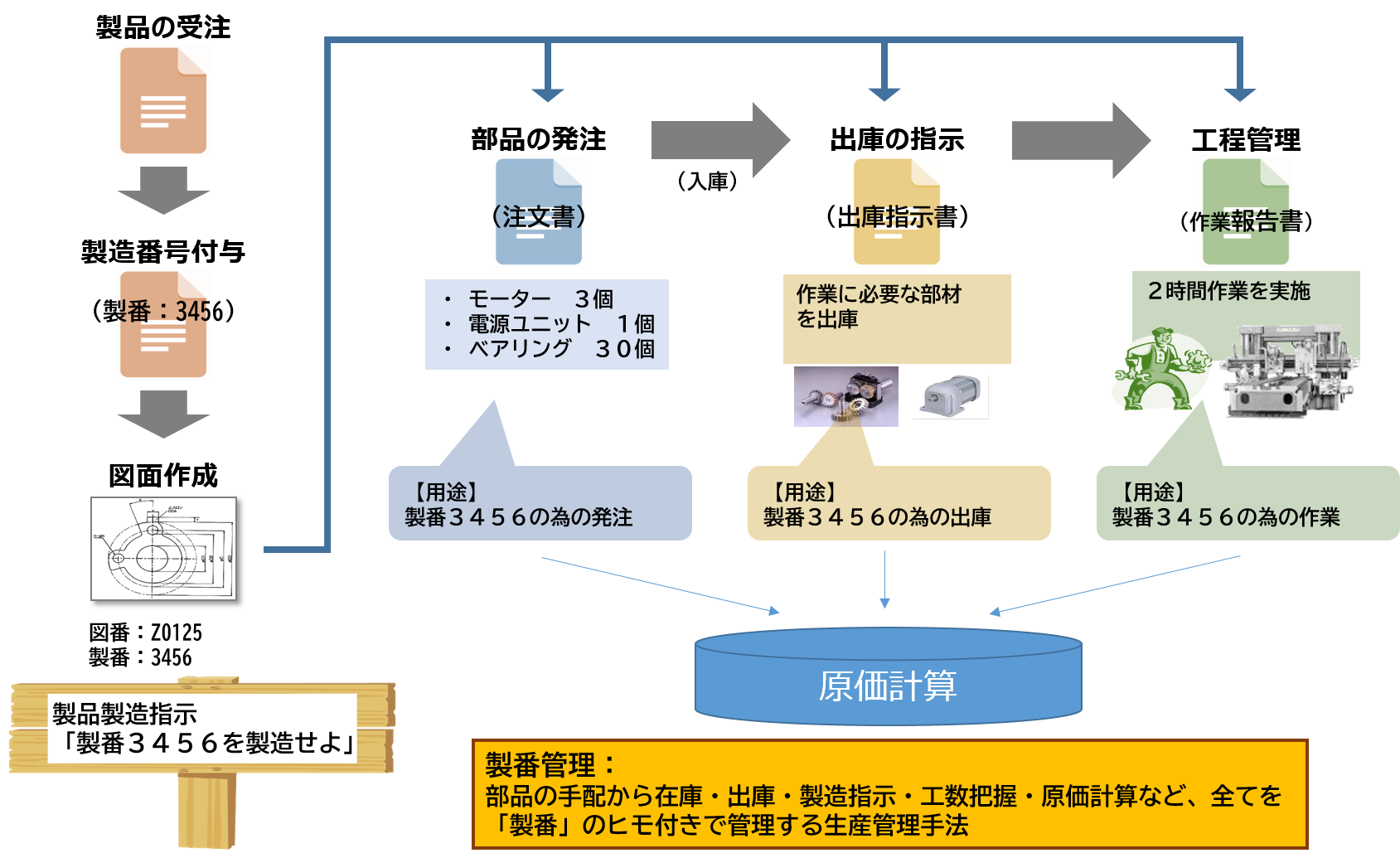
2.MRPと製番管理の比較
製番管理と比較される資材計画方式にMRP:Material Requirements Planning(資材所要量計画)と呼ばれるものがあります。夫々の特徴を以下にまとめておきます。
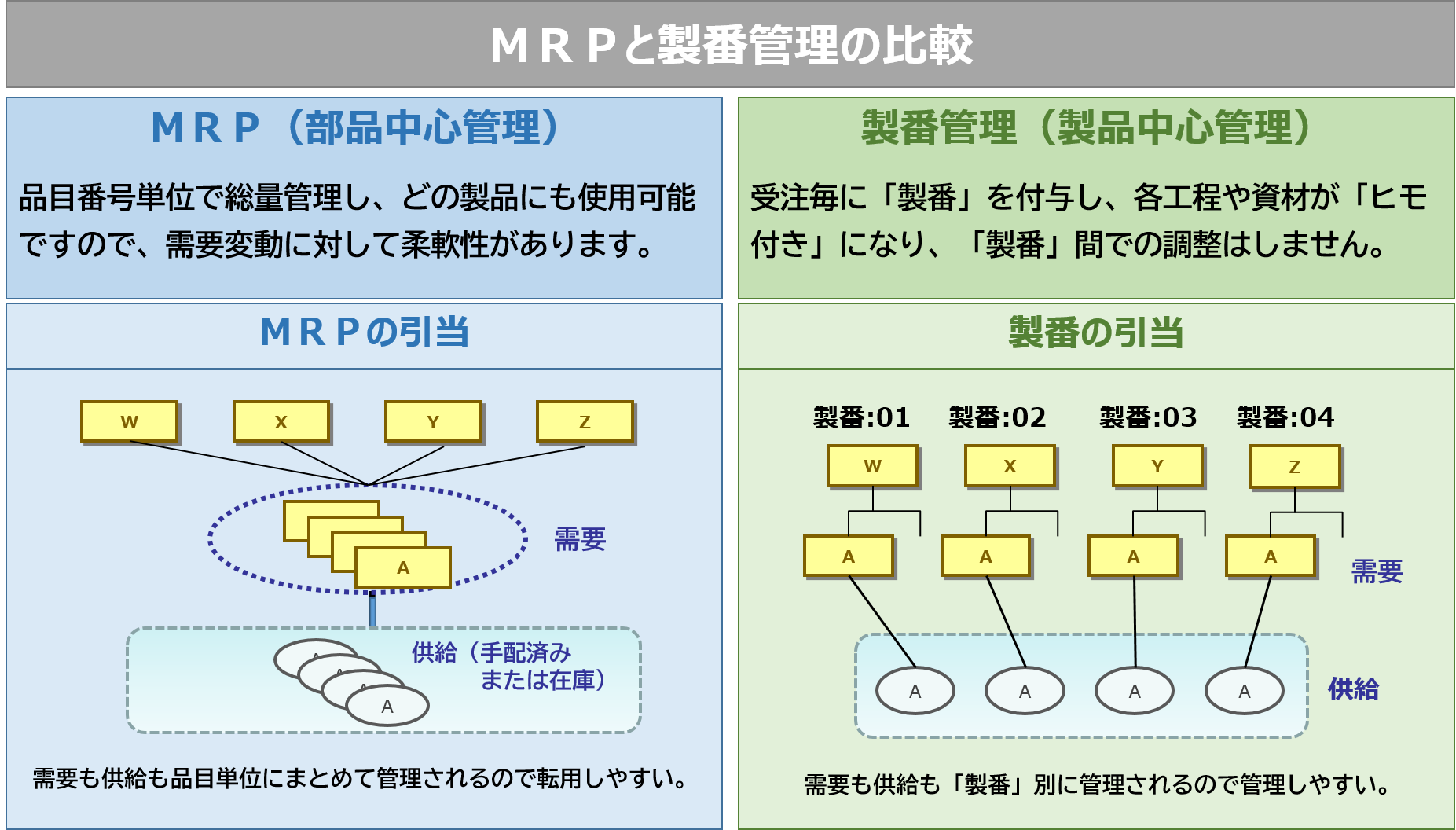
どちらの方式でも製品の需要に基づき部品表(BOM:Bill Of Matrial)を使って必要部材の手配を行う意味においては同じ様な機能が必要ですが、管理単位がMRPでは品目番号ごとであり、製番管理においては品目番号と「製番」が管理単位になっています。
3.製番管理の種類
製番管理といっても号機単位の個別管理ばかりではありません。様々な種類がありその目的や適用範囲について具体例を紹介します。
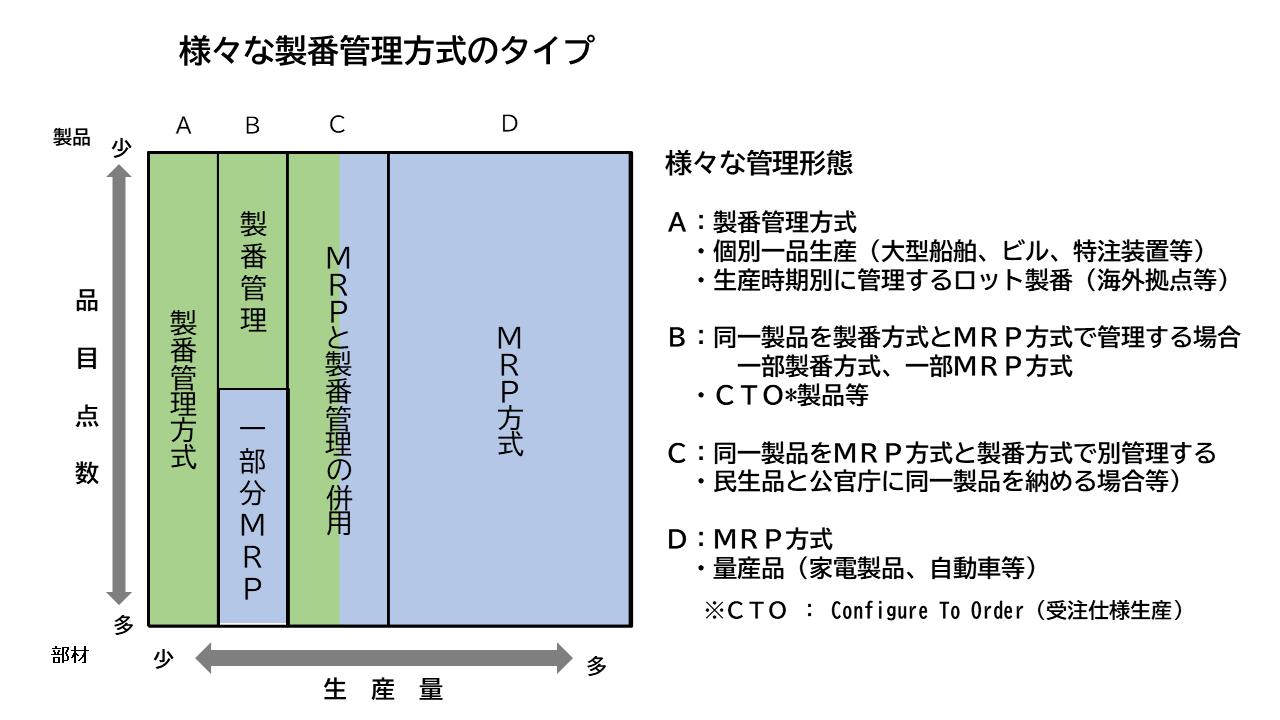
A)は典型的な製番管理方式の例で、BOM(部品表)における末端の品目から製品に至るまで、1つの「製番」で紐付き管理するもので、一品一様の個別受注生産製品でよく使われます。
又量産品の場合でも海外生産拠点などで日本から供給する重要部品に対して生産時期(生産月、週あるいは日)ごとにロット番号を付与し、あたかも製番のような取り扱いをおこない、生産時期毎の需要と供給がまとめられ、在庫管理を簡素化するために「ロット製番」が使われることもあります。
B)個別受注生産品目の部材の中にはわざわざ個別管理をせずに、まとめ買いや他の「製番」と共有する方が良いものもあります。例えばボルトやナットといった汎用性の高い部材などです。
BOM(部品表)の末端の部材はMRP方式でまとめ買いをし、最終組立に近いところからは受注別に「製番」管理を行い、「製番」とMRPの良いとこ取りをすると云う都合の良い方式です。
設計段階から生産工程を意識して共通性の高い部分とカスタマイズすべきところを分けておく必要があります。
C)製品としては民生品と同じものでありながら、業務用の場合、例えば官公庁等から、その製品がどのように造られたのかを明確にするため部材の調達から在庫、生産工程までのきめ細かい管理が要請されることがあり「製番」で管理する事があります。
D)一般的なMRPによる部材の調達方式です。
製番管理といっても様々な管理方法があり、ひとつの会社でひとつの方式と言うわけではありません。
MRP方式と製番管理方式の両方の製品を持っている会社も少なくありませんが、夫々の方式にあった複数のシステムが必要なのでしょうか?
次回はこの点について言及したいと想います。